The optimization of heat dissipation in electric mobility
(Edited by Luca Lenardi, CEO of Atra S.r.l.)
The constant growth of electric mobility continues to revolutionize the automotive industry and its vast supply chain, reaching more than 39.000 electric and hybrid vehicles registered in 2022 in Italy.
This transformation is leading to an increase in the production of batteries, electric motors, heat sinks, integrated circuits, inverters, power modules: elements that require increasingly sophisticated solutions for managing heat dissipation. In fact, the longevity of the components and their ability to function correctly in all conditions of use and in safety depend on it. Just think, for example, that reducing the average temperature of a battery by 10°C means doubling its operating life.
How the dispensing of thermoconductive resins helps to increase the life of the components
The preformed adhesive pads that are still often used in small jobs have some contraindications. Firstly, it is an expensive material and not always consistent in thickness. Furthermore, it must be applied mechanically, by pressure, which can be detrimental to electronic components. It cannot be thinned beyond a certain limit, otherwise it will be impossible to handle it and it does not adapt flexibly to irregular substrates. More importantly, it is not suitable for certain crucial production sectors: for example, it is not compatible with the stringent 5G or 6G tests in the automotive sector, because it does not guarantee stability over time with respect to the vibration of the running vehicle.
In the light of all this, the use of liquid dissipation substances or thermally conductive pastes is much more effective and efficient. For example, by dosing appropriate quantities of these resins between the battery modules and their housing, the thermal resistance of the latter can be reduced by up to 40-50%, significantly lowering the overall temperature of the battery pack.
The mechanical and heat dissipation properties guaranteed by these resins are crucial for the entire automotive sector: in fact, they also find applications in on-board networks, in the management of electronic components, in LED areas, in sensor technology, in the charging infrastructure and in inverters. This is the type of highly specialized processing that has favored the entry into the field of manufacturers of precision dosing systems.
Which are the technical challenges in using these particularly abrasive resins?
The ability of a thermally conductive resin to conduct heat is conferred by the high concentration of fillers, usually aluminum oxide, silver or boron nitride. Fillers are irregular fragments, spheres or cubes, often have very high levels of hardness and sharp-edged profiles. For this reason, as the dissipative properties of the resins increase, their specific weight also increases.
Today the market is moving towards silicone, epoxy and polyurethane resins, equipped with fillers that bring their specific weight to over 3.5 g/ml, well beyond that of aluminium. Polyurethanes reach a dissipation coefficient of 1.6 W/°K m, and range in temperature ranges from -50°C to +160°C. Epoxy and silicone resins reach a thermal conductivity of over 4.5 W/°K m. There are also special resins with silver or gallium fillers that reach respectively up to 8 or even 13 W/°K m, but their costs are prohibitive for the industrial scale and their use is limited to highly specialized productions.
The presence of abrasive fillers poses enormous challenges for the delivery systems of these resins. Almost every type of pump used undergoes serious mechanical wear which leads to a progressive reduction in delivery accuracy, increasing maintenance costs and significant periods of machine downtime. To minimize these problems it is essential to use the best performing preparation and dispensing technologies. Gear pump systems, for example, are unsuitable for handling abrasive materials, as mechanical interference would quickly degrade the operational capability and life of the pump. Cavity pumps, on the other hand, represent a good dispensing solution for this type of resin, but involve much higher maintenance costs than piston dosing technology. The state of the art for the dispensing of mono and bi-component resins for heat dissipation is represented by piston volumetric dosing systems with disposable static mixer, capable of combining precision and operational continuity, with decidedly reduced costs and maintenance times compared to all other available technologies.
The importance of relying on a partner capable of providing integrated solutions
For over 30 years Atra, working in close contact with the customer, has been designing and manufacturing systems for dispensing mono and bi-component resins for complex industrial applications in atmosphere and vacuum, where the ability to integrate these technologies within the customer's production lines in effectively and efficiently, makes the difference. The effectiveness of application solutions does not pass only through the hardware aspects of the machine, but increasingly also through the customization and integration of the software within the customer's IT infrastructure. This is why all the machines are native 4.0, equipped with an integrated AP, and are able to communicate with management systems (MES, ERP, ...) according to internationally validated protocols, such as HTTPS or SSH, and military grade encryption standards AES-256.
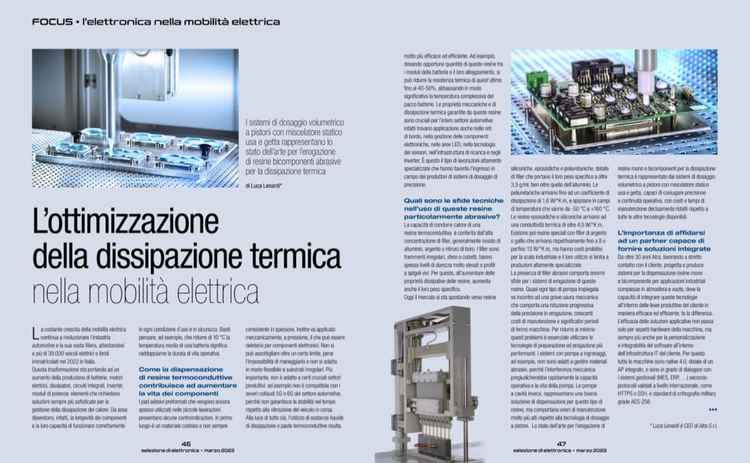