In the context of the risk due to the presence of potentially explosive atmospheres in a workplace, several years ago the European Union has adopted two important directives that define the minimum health and safety requirements.
"ATEX" is the acronym of the two French words "Atmosphere Explosive" and defines an atmosphere with the presence of a mixture of flammable substances in the state of gas, vapours, mists or dusts which, under certain conditions of pressure and concentration, can ignite and rapidly spread combustion to the flammable mixture. The explosion can only occur in the presence of an ignition source and when the concentration is within the explosive range in mass or volume of the substances, between the minimum (LFL) and maximum (UFL) limits.
Beyond the oil and mining world, there are many contexts that require an ATEX approach, as they present explosive atmospheres potentially in contact with hot surfaces, electrical material, electrostatic charges, mechanical sparks or other. It has been estimated that about 70% of industrial environments present problems of this type. Just think, for example, of agri-food, textiles, metalworking, vehicle spray painting, the production of chemicals, the wood industry or all environments that use pressurized gas. ATEX certification is intended to prevent danger in all these environments.
Atra has over thirty years of experience in resin dosing technologies and corollary processes such as plasma treatment, polymerization furnaces and automation. These processes are a crucial part of electronic and electro-mechanical production even in the ATEX environment, since the encapsulation in liquid resin perfectly isolates the electronic components, separating them hermetically even from the most difficult work environments.
For the Oil & Gas industry it is essential to strictly comply with the ATEX directive in all processes: sampling, compressors, control systems, control instrumentation, fracking, distribution system, transformers, etc. ATEX products in the Oil & Gas sector are a very interesting field for Atra, which works with important national and international customers by supplying resin dosing systems used in the production of products in the explosion-proof field, to build and seal insulator or feedthrough components. The company works alongside customers to ensure that products comply with safety regulations and can quickly reach their target markets.
In the last century, the electrical systems designed for environments with danger of explosion were mainly made with pipes of the "freez moon" type and the inlet and outlet terminations of the containers were made with simple locking joints. The advent of the cable-gland has radically changed the method of plant engineering, facilitating installation and giving the possibility to recover the cable in the event of restoration work. The modern ATEX connecting elements are sealed using a two-component resin with high technical and mechanical characteristics which is applied to each conductor. The elements thus treated can conduct energy even at high potentials, up to 1,000 A, allowing electrical contact between bodies inside or outside the protected system. This is fundamental, for example, in the distribution of electrical cables in the oil, chemical and pharmaceutical fields. The protective piping that leads the cables through dangerous environments inevitably has joints, T or Y branches, elbows: inside all these fittings, usually in aluminium, Atra intervenes with polyurethane resins with appropriate technical and mechanical characteristics. This prevents any infiltration of flammable and explosive gases from continuing along the entire pipeline. Atra systems thus sealed in the field pass tests with pressures up to 30 bars and 130 °C.
This technique can be applied to all the main components of an electrical system with ATEX characteristics: fittings, adapters, closing caps, 90 ° bends, opening bends, sleeves, locking fittings, rigid and flexible pipes, explosion-proof junction boxes, watertight enclosures and cable glands.
Another crucial sector in the ATEX field is industrial lighting. For an important customer in this sector, for example, Atra has created a system for the production of lamps for work areas in environments with a high risk of explosion. It is a resin island complete with dosing head and material feeding system. The island performs the automatic perimeter resin coating of the lamp profile, allowing the explosion-proof glass to be hermetically fixed to the body. Atra used a DOI dosing head that sweeps over an XYZ work island and takes the single-component resin from a pressing plate feeding unit. The system includes two benches equipped for the preparation and handling of the workpiece pallets by means of guides and rollers.
The proposal was based on an AERIA process module with integrated dosing in atmosphere, customized with an X axis increased to 1500 mm of stroke, according to customer specifications. The system guarantees maximum precision and reliability thanks to the dispenser positioned directly on the axis, near the dispensing nozzle, without long moving pipes between dosing and mixing. The XYZ axes are interpolated with the control motor of the dosing pump, allowing the best distribution of the material even on curves and corners. The system includes an integrated centesimal weighing system for checking the correct flow rate before starting processing.
All the resin systems designed by Atra are "4.0 ready", designed from the outset to interface with ERP, MES and other machines of the pre-existing line. In particular, the advanced technological features of this dosing system have allowed the customer to certify it according to the requirements of the Industry 4.0 Plan, allowing to obtain a tax credit which has reduced the purchase cost by 50%.
Over the years Atra has developed a growing vocation as a consultant to solve specific production problems. The company seeks on the market the materials, technologies and experiences closest to the customer's needs, customizing them and building the most suitable solution for each specific production process. Often it is a question of inserting into a new field some solution already tested in a different sector. For example, the company has come to use some technologies matured thanks to the initial experiences in the optical field in the dosage of resins for the automotive sector. This transversal strategic ability is one of the characteristics that distinguishes the company's activity on the market.
Watch the full video of the system on our YouTube channel.
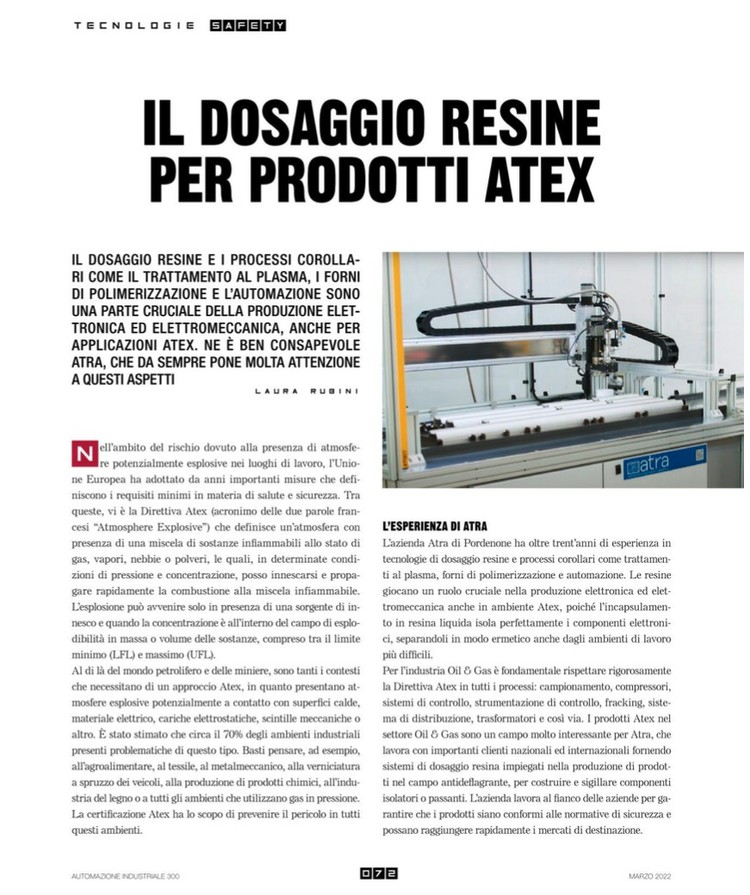
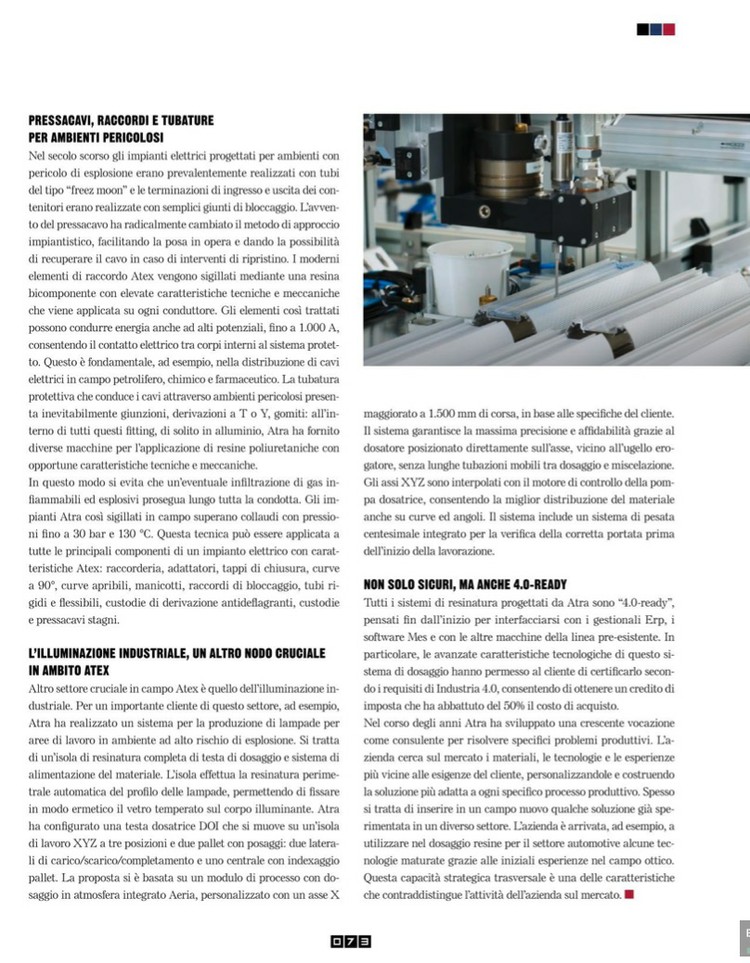