A new article about Atra appeared in the April issue of PCB Magazine. It describes our fully automatic island for polyurethane resin dosing via an anthropomorphic robot. The system has been built for an important customer of ours, an Italian company that provides advanced electronic engineering services.
In the system designed by Atra, two pressure tanks for mixing and feeding resin and hardener feed a Scheugenpflug DOS P016 volumetric dosing head. The PCB is taken from the pallet by a Kawasaki 6 degrees of freedom robot featuring pneumatic manipulators. The arm moves the piece under the dosing head, allowing the needle to deliver resin in more than fifteen different point, linear and curved positions, on both sides of the PCB, without time constraints. An optical sensor checks the presence of the piece and automatically manages any deviation. Two calibration units check the correct position of the dispensing nozzle in real time. The dosing head is managed by the Scheugenpflug SCP200 process controller. In this application, the resin performs the function of additional fixing on the PCB of components with a high centre of gravity, ensuring the necessary resistance to mechanical stress.
On our YouTube channel, there is an interesting video showing how the system working.
Here is the complete article:
"The level of automation is constantly increasing in all industrial sectors. The market has now widely understood that speed, traceability, quality control and integration according to the parameters of Industry 4.0 bring advantages that largely offset the higher initial costs of the production system. Whether in the automotive, electronics or medical industries, automated manufacturing ensures the highest level of performance and efficiency. Precision resin dosing industry is no exception.
Atra is a Pordenone-based company that has been engaged for over 30 years in R&D of innovative systems for the resins preparation and dispensing. Its systems are used for potting, impregnation, gluing and the production of FIPFG (Formed in place Foam Gasket) gaskets for all major industrial sectors. Over the course of its ten-year exclusive collaboration with partners Scheugenpflug (dosing), Inocon (plasma) and perfecdos (micro-dosing), Atra has accumulated extensive experience in automation, from component recognition to position detection, from surface treatment to systems quality control. What distinguishes Atra on the dosing systems market is the care taken in the software design of the machines, the implementation of the technologies required by Industry 4.0, as well as the ability to create extremely versatile systems with respect to online integration. All Atra resin dosing systems are scalable and based on a state-of-the-art modular system. Tested components and reliable processes help the industrialization of the system, specifically designed according to the customer's needs.
The precision dosage of the resins plays a pivotal role in the processing of printed circuits. Encapsulation resins are typically two-component systems in which resin and hardener are mixed to form a cross-linked polymer. The substances are used in the last phase of the industrialization processing, to protect electronic devices and connections working in the most difficult operating conditions. The materials are used to "encapsulate" the individual components or "submerge" the entire unit, ensuring excellent protection in the event of prolonged exposure or immersion in water and/or aggressive chemicals. Often also used in high voltage electronics and in ATEX explosive environments, the resins also provide a total dielectric layer to prevent arcing.
Automation of the resin processes involves up to eight macro-phases:
- Sensors, light curtains and camera systems for detecting the temperature and position of the workpiece allow accurate handling and protect against accidental damage.
- The careful cleaning and activation of the substrate surfaces guarantee the durability and reliable operation of the component. These can be done through plasma, UV rays, contactless cleaning via compressed air nozzles, preheating and drying ovens.
- Regarding the polymerization and crosslinking of materials, there is a wide range of systems that cover any type of resin used for potting and satisfy every process requirement. The main ones are hot air and IR polymerization (continuous oven or batch oven), or through UV rays, in the case of transparent resins.
- Among the handling systems we can mention conveyor belts, pick-and-place applications, automatic palletizers, up to industrial robots.
- Among the different bonding technologies, the main processes involve self-leveling and thixotropic adhesives.
- The integration of adequate quality control systems in the production phase (such as automated optical inspection and leak test) reduces the frequency of errors, ensuring high quality components and a reduced number of rejects.
- The different identification processes of the piece range from labeling to laser and transponder marking.
- Finally, industrial systems require reliable communications and networks. To ensure first-rate traceability and for documentation purposes, Atra provides numerous solutions: MES integration, process data interface (PDI), traceability systems, SMEMA interface and statistical process control (SPC).
Up until the 1990s, a typical SMT assembly line used two different types of pick & place machines in sequence that could place up to 53,000 parts per hour, which is nearly 15 parts per second. Since it was the PCB that moved, not the machine, only light parts could be positioned in this way that would not be loosened by the violent movement of the workpiece. From the high-speed machine, the PCB then moved on to a precision positioning machine. These systems could handle larger or more irregularly shaped parts, such as large integrated circuits or packaged inductor coils and potentiometers.
The following generation of modular, multi-head and multi-gantry all-in-one machines could feature interchangeable heads depending on the product to be built, could position components from 0.4 × 0.2mm to 50 × 40mm, with speed of theoretical up to 136,000 CPH (components per hour). The fastest machines could have speeds of up to 200,000 CPH.
Starting from the first decade of the 21st century, there has been a great change in the approach to the sector, with a greater focus on process software applications. With new applications such as POP and wafer-to-substrate placement, the industry is now moving beyond conventional component placement. The most modern pick & place machines place at very high-speed components with minimal dimensions, indistinguishable without the aid of a magnifying optics. Not only have the assembly systems evolved according to a curve that has risen almost exponentially, but also the consumables have improved their characteristics, reaching the point of guaranteeing performances that have grown more and more year by year in terms of yield and quality. lasted. With the recent changes in the economic climate, the demand for SMT positioning is now focusing on the versatility of the machine to cope with short runs and rapid production changes.
In line with these needs for flexibility and efficiency, Atra has created a fully automatic island to dose polyurethane resin on PCBs using an anthropomorphic robot. The customer is an important Venetian company that provides advanced electronic engineering services: the company manufactures assembly lines for SMT components, SPI systems for 3D inspection of solder paste deposits, AOI systems for Automated Optical Inspection, automatic assembly lines for PTH and Faston components, robotic cells for the automatic assembly of “Odd-Shape” components, X-RAY inspection systems, ICT and functional testing equipment, testing equipment for user interfaces with Touch and Graphic Display technology. In the system designed by Atra, the pressure tanks for mixing and feeding resin and hardener feed a Scheugenpflug DOS P016 volumetric dosing head. The PCB is taken from the pallet by a Kawasaki 6 degrees of freedom robot with pneumatic manipulators. The arm moves the piece under the dosing head, allowing the needle to deliver resin in over fifteen different point, linear and curved positions, on both sides of the PCB without time constraints. An optical sensor checks the presence of the piece and automatically manages any rejects. Two calibration units check the correct position of the dispensing nozzle in real time. The dosing head is managed by the Scheugenpflug SCP200 process controller. In this application, the resin performs the function of additional fixing on the PCB of components with a high centre of gravity, ensuring the necessary resistance to mechanical stress."
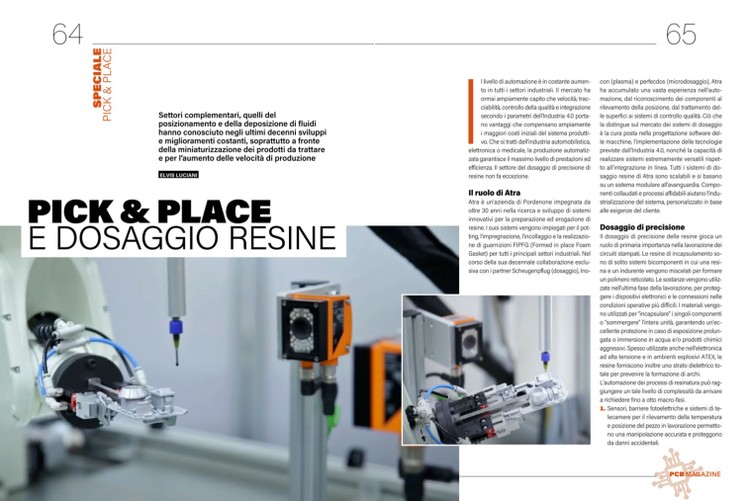
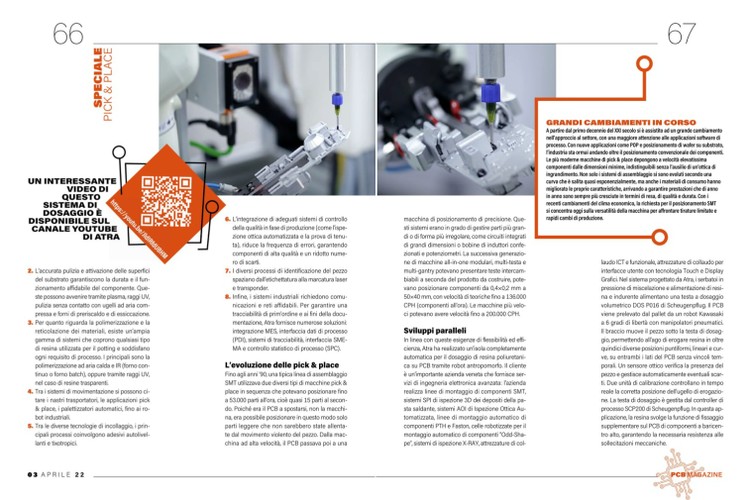