Resin dispensing solutions and digitization of the production line
(Edited by S. Bongiorno, Head of IT of Atra S.r.l.)
IoT technology makes it possible to adapt production systems in real time and to carry out analyzes on Big Data. Furthermore, the constant monitoring of production ensures greater speed, even between prototyping and realization. Finally, the interconnection of machines, people and information makes it possible to improve performance and reduce waste, also from an energy point of view. However, in order for the benefits of the IIoT to be realised, an enabling infrastructure is needed towards which to direct the collected data, transform it first into information and then into actions. The best solution is the Cloud.
Since the new "smart factory" is an enterprise whose machines are able to read the surrounding environment, communicate with each other and make autonomous decisions, the connection is the real key point. To access the machine remotely, thus using it as an access point, Atra prefers Wi-Fi in the WLAN environment according to known technologies (IEEE 802.11b/g/n). This in particular can be appreciated for access to man-machine interfaces and for interfacing with management systems, where response time is crucial. Its systems are equipped with an integrated AP, which allow you to interact with the machine without the need to "insert" it into the production Lan/VLan. As far as communication with actuators and sensors is concerned, apart from the use of Rfid solutions for tracking and managing parts, for now the company has preferred not to use a Wi-Fi solution because the response time is generally higher and the signal is often disturbed.
Highly integrated hardware and software architecture
Atra's systems represent an extremely effective fusion of hardware and software. It is an architecture aligned from the outset to the philosophy of Industry 4.0, in which all systems are connected
in the Cloud to a central server that manages communication, data collection and external inputs. The company has studied a client/server architecture on the Internet model: the machine is a server to all intents and purposes, while each external interface works as a client, accessible simultaneously to various operators. The client can be a web interface for an operator panel, but also a management system, a Mrp or a Mes. Another interesting aspect is that the company has developed its electronics and software in a modular way: it is possible to obtain greater versatility of use by extending the packet system, i.e. by adding general purpose I/O cards, valid for any industrial application.
This versatility is also made possible by the availability of a large number of communication protocols, digital and analog inputs and outputs.
The search for an increasingly perfect fusion between hardware and software continues thanks also to an IT architecture expressly aligned with the philosophy of Industry 4.0. All the proposed solutions are connected in the Cloud to a central server which manages communication, data collection and external inputs. The client/server architecture was developed on the internet model: the machine is a server to all intents and purposes while each external interface works as a client, accessible simultaneously to different operators. The client can be a web interface for an operator panel, but also a management system, an MRP or a MES.
Each system is tailored to the customer's needs, with all and only the necessary components: this cuts costs and eliminates superfluous parts, subject to possible breakage and maintenance. The entire machine is lightened from a software, hardware, mechanical and electronic point of view. The man-machine interface is also simplified, free of superfluous commands.
The usability of user interfaces as an enabling factor
Even the user interface, designed for touch devices, is focused on the operator and has a modular structure that allows you to easily adapt to the specifics of each plant. Easy to understand, it is process-oriented and offers operators solutions to keep the most significant parameters under control at all times. Using the latest web technologies, Html5 and CSS3, it is based on Google's Material Design guidelines, guaranteeing ergonomics and accessibility to the operator. The "responsive" implementation allows adaptation to a wide range of devices (in addition to the panel on the machine) such as industrial monitoring tablets and laptops for programming.
All interfaces are "fully responsive", i.e. they adapt dynamically and automatically to display on a computer, tablet or mobile phone. This detail also improves the user experience, which can always display the elements of the interface in a coherent way.
Use of machine data for predictive maintenance
Modern IIoT (Industrial Internet of Things) devices and applications, together with the availability of advanced analytical tools and the emergence of artificial intelligence and machine learning technologies, today make it possible to integrate sensors of 'each type, and to network such equipment, and then continuously monitor their operating status. On the basis of the collected data, predictive models are elaborated which allow optimization of the maintenance strategy.
Thanks to the digital transformation of companies and the growing availability of data on the state of the physical infrastructure, predictive maintenance of production systems is rapidly emerging as the most effective of all maintenance modalities.
An all too often overlooked benefit of predictive maintenance is the ability to generate a historical database of equipment performance that can be leveraged to increase the accuracy of future predictions. The CMMS generates and manages the database of all the events that occur on machinery and systems, corrective and repair interventions, inspections and calibrations, all essential information for making forecasts. To ensure maximum resource effectiveness, the CMMS analyzes both repetitive failures (which are the best known) and random failures (which represent the largest percentage).
Since the basis of predictive maintenance is the collection of information in real time on the operating conditions of the machines and the sending of data to a central unit, the coupled IIoT (Industrial Internet of Things) and CMMS (Computerized Maintenance Management System ) constitutes a strategic element for companies.
The conditions of the machinery are monitored through the use of sensors installed on critical parts and the detected deviations are transmitted to the CMMS which will identify and quantify. For example, it is possible to acquire data relating to temperatures, vibrations, noise, lubrication levels and many other quantities useful for identifying variations with respect to the standard.
Thanks to these systems, companies can enhance and simplify the sharing of information at all levels and, at the same time, reduce waste or production anomalies. Telemetry and remote control of the machines allow you to monitor the progress of production at any time, regardless of the physical distance from the plant.
The importance of relying on a partner capable of providing integrated solutions
For over 30 years Atra, working in close contact with the customer, has been designing and manufacturing systems for dispensing mono and bi-component resins for complex industrial applications in atmosphere and vacuum, where the ability to integrate these technologies within the customer's production lines in effectively and efficiently, makes the difference. The effectiveness of application solutions does not pass only through the hardware aspects of the machine, but increasingly also through the customization and integration of the software within the customer's IT infrastructure. For this reason, all machines are native 4.0, equipped with an integrated AP, and are able to communicate with management systems (MES, ERP, ...) according to internationally validated protocols, such as GRPC HTTPS or SSH, and military encryption standards grade AES-256.
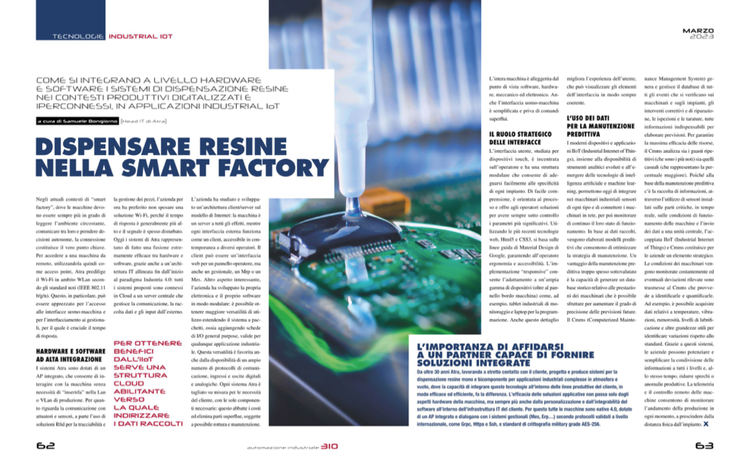